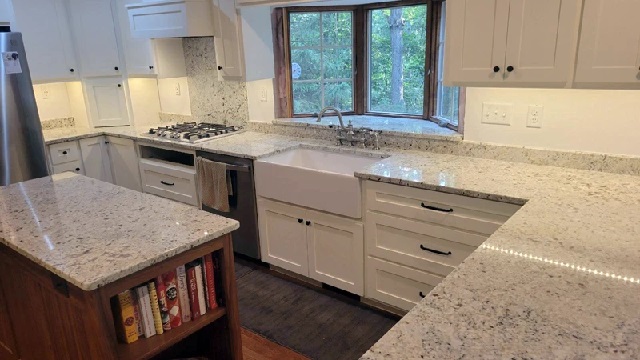
Introduction
Quartz worktops have indeed become a favored choice for contemporary kitchens and bathrooms, and their popularity can be attributed to a combination of qualities that set them apart in the world of countertop materials. These qualities, including remarkable durability, non-porous characteristics, and an elegant appearance, have made quartz worktops highly sought after in the realm of interior design. However, the process of transforming raw quartz crystals into the polished worktops that adorn countless homes is a fascinating journey that involves several intricate steps.
The journey begins with the extraction of raw quartz crystals from quarries or mines. Quartz, one of the most abundant minerals on Earth, is typically found in large deposits, and these deposits are carefully excavated to acquire the highest-quality quartz crystals. Once extracted, the quartz crystals are transported to a processing facility where they undergo a series of transformative processes.
One of the most critical steps in the production of quartz worktops is the crushing and grinding of the quartz crystals into a fine, uniform powder. This powder serves as the foundation for the worktop’s composition. It is here that pigments and resins are added to the quartz powder to imbue the material with color and provide the structural integrity needed for a durable surface. The mixture is carefully controlled to ensure consistency and quality. The addition of resins is particularly crucial as they play a vital role in binding the quartz particles together and imparting the non-porous nature that makes quartz worktops highly resistant to stains and moisture.
After the mixture is perfected, it is poured into molds to create slabs of varying thicknesses and sizes, depending on the intended use. These slabs are then subjected to an intensive curing process that involves heat and pressure. This process not only hardens the material but also helps the resins bind the quartz particles together, resulting in a solid, resilient surface.
Once the slabs have cured, they are meticulously polished to achieve the characteristic lustrous finish that is synonymous with quartz worktops. Skilled craftsmen use precision equipment to create a smooth and reflective surface that showcases the natural beauty of the quartz crystals. The final product is not only stunning but also exceptionally durable and low-maintenance.
In conclusion, the journey from raw quartz crystal to the polished worktop that graces modern homes is a complex and carefully orchestrated process. It involves mining, crushing, mixing, molding, curing, and polishing, each step contributing to the creation of a stunning and enduring surface that has become a staple in contemporary interior design. The allure of quartz worktops lies not only in their aesthetic appeal but also in the meticulous craftsmanship and engineering that goes into their production, making them a functional and elegant choice for kitchens and bathrooms.
- Sourcing Raw Quartz
Quartz crystals are mined to kick off the adventure. Quartz is extracted from the earth and is one of the hardest minerals on the planet. Quartz is mined extensively in countries like Brazil, the USA, and India. Large slabs of quartz are cut from the mine and shipped to the processing plant.
- Inspection and Cleaning
The quartz pieces are checked for defects as soon as they enter the facility. Only the purest, most flawless parts are chosen. The pieces are then washed and dried to get rid of any remaining dust, dirt, or other contaminants.
- Crushing and Grinding
After being washed and dried, the quartz is crushed into powder. Modern equipment is used in this method to standardize granule size. The granules become a powder after being finely processed. The quartz countertop is primarily made of this powder.
- Mixing with Resin and Pigments
Despite its hardness, quartz alone is not a good material for countertops. To make it flexible and moldable, resins must be added to the mix. Quartz typically makes up 90–95% of the mixture, with resin making up the remaining 5- 10%.
Pigments are also introduced at this step. These pigments are responsible for the wide color palette of quartz countertops. The range of colors is enormous, including everything from pure white to jet black.
- Molding into Slabs
Quartz, resin, and colors are mixed together and then poured into molds. The mixture is pressed into molds of varying thicknesses to create slabs. After that, the slabs go through something called “vibrocompaction.” The slabs are made dense and air-free through this method of compacting them using vibration and pressure.
- Curing the Slabs
After that, the slabs are transferred to a kiln for the curing process. In this step, they are baked for a predetermined amount of time at a high temperature. This procedure causes the resin to become more rigid, which in turn binds the quartz particles together and confers strength and durability on the slab.
- Polishing and Quality Control
Polishing the slabs once they have been cured produces the ideal finish on the material. Polishing equipment of the most recent generation assure consistency and excellence, whether the desired result is a glossy shine or a matte finish.
Every slab is subjected to exhaustive quality inspections. The inspectors search for flaws like as cracks, defects, and color and finish variations that don’t match up. Those who are successful after going through all of these rigorous tests will advance to the next step.
- Cutting to Size
The slabs are sliced into the needed dimensions for kitchen countertops, bathroom vanities, or any other use, according on the orders and specifications provided by the customer. Innovative cutting equipment guarantees precision and accuracy, resulting in a product that is a flawless match for the end-user.
- Final Inspection and Dispatch
One last quality control check is performed on the finished quartz worktop before it is shipped. This guarantees that the final product satisfies the most stringent requirements pertaining to its quality and level of craftsmanship.
After being inspected and given the go-ahead, the quartz worktops are carefully wrapped and then shipped to the houses of retailers, builders, or homeowners.
Conclusion
The process of transforming a raw quartz crystal into a finalized worktop involves a harmonious combination of natural aesthetics and human innovation. Upon observing a quartz worktop in the future, one will develop a heightened level of admiration for the intricate and precise procedures involved in its creation. The selection of a quartz worktop, whether based on its durability, aesthetic appeal, or both, serves as a remarkable demonstration of the advancements achieved in the field of production.